Project Summary
Mohawk Valley Water Authority, NY
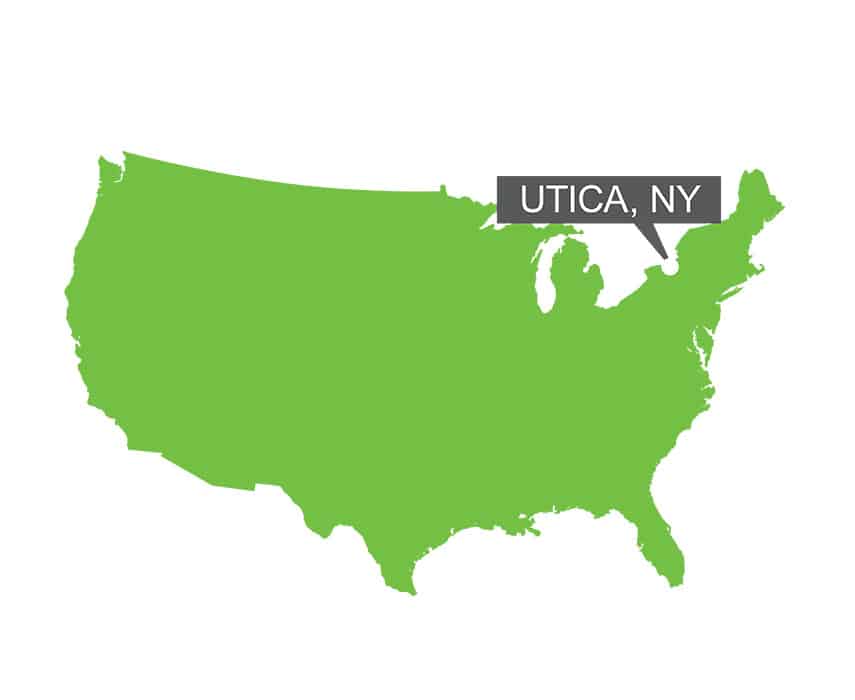
Type of Project
Spray-in-place pipe rehabilitation
Results
- Considerable time and cost savings
- Greater system reliability
- Elimination of disruption and inconvenience characteristic of traditional open cut process
- Potential hydraulic improvement including increased flow for fire protection and other needs
Headquartered in Utica, New York, the Mohawk Valley Water Authority (MVWA) is a regional agency that provides drinking water to approximately 128,000 customers throughout 18 municipalities in Oneida and Herkimer Counties.
Responsibility for MVWA’s water system falls on the shoulders of its Director of Engineering, Eric. G. Schuler, P.E. Since he joined the organization, one of Schuler’s goals has been to address its rehabilitation and replacement plan. “One of my goals coming on board was to figure out a sustainable way for us to not only rehabilitate, but also replace existing components in our system. Obviously rehab is one of those tools,” he notes.
The plan includes proactively rehabilitating MVWA’s water mains, starting with rehabbing 3,500 feet of 6” and 8” cast iron pipe using USG Water Solutions (USG) Spray-in-Place Pipe (SIPP) solution.
Leveraging the power of SIPP
With an extensive background in engineering, Schuler is familiar with most rehab technologies including SIPP and said that it had been under consideration for some time. “This was our first SIPP rehab application, and it was a good start for us,” he says.
MVWA’s staff, some of whom have worked at the utility for 30+ years, had kept good track of data to help shape the plan, including main break frequency per street or per stretch of pipe segments from intersection to intersection, the age of the pipes, and the pipe material. The three streets chosen were at the top of the list, with pipes ranging from 70 to 100 years old. According to Schuler, having hard data on which to base decisions and a revised capital program laid the groundwork for creating and implementing a plan, and setting a process and budget going forward.
“
Cost savings and time savings were huge benefits, but also hopefully system reliability. The three streets we ended up on were at the top of the list for being able to do SIPP. It was an area that has historically been leaky and had frequent breaks, with pipes ranging from 70 to 100 years old.
— Eric. G. Schuler, P.E., Director of Engineering, MVWA
SIPP – a trenchless, long-lasting solution
USG’s SIPP process is an efficient and long-lasting trenchless pipe rehabilitation solution consisting of four steps.
- Once the utility agrees on the two access point locations, an access pit is dug one foot below the host pipe at each end of the SIPP run. A three-foot section of the host pipe is removed to allow access to the relining equipment. Using closed-circuit television (CCTV), USG confirms the section of pipe to be restored.
- The pipe interior is then prepared by drag scraping, and/or hydro-jetting to create a clean, smooth dry surface.
- A second CCTV inspection is conducted to determine if there are any leaks, infiltration or repairs that are needed outside of the SIPP scope of work to ensure that the pipe is properly prepared for application of the epoxy coating. Any repairs needed to address current piping issues are undertaken without the need for additional excavation.
- The epoxy coating is then applied via a spray nozzle attached to a state-of-the-art, computer-controlled robotic spray rig. The 2-part component epoxy material is ANSI/NSF Standard 600 approved for potable water supply. Once the coating has cured, USG conducts a final CCTV inspection to make sure the lining is correct. The sections of pipe that were removed at the access points are reassembled, and the utility proceeds with the chlorination/disinfection before system restoration.
The cured epoxy creates an internal seal inside the pipe, preventing leaks and providing long-lasting protection against future corrosion and biological buildup in the water main. Additionally, SIPP extends the service life of water or sewer pipelines, reduces the frequency of maintenance, and minimizes repair costs and system down-time.
This rehabilitation technology works on pipes made of different materials and ranging from 4 inches to 36 inches in diameter.
Benefits of SIPP
The MVWA SIPP project not only yielded cost savings but also eliminated the disruption and inconvenience characteristic of the traditional open cut process. Additionally, it also considerably shortened the time needed to complete the rehab work.
While these benefits are important to every utility, they are also important to the utility’s own customers.
In this case, the location of MVWA’s initial SIPP project placed it squarely in a residential area. SIPP allows the utility to expedite the repair or rehab work, so it has a minimal impact on residents. Instead of facing a lengthy open cut job, SIPP required only two small cuts, and USG was able to rehab the main in between them quickly and efficiently.
Schuler noted that, in addition to considerable time and cost savings, other benefits include greater system reliability and potential hydraulic improvement. The reliability issue was critical as the rehab took place in an area that, historically, was subject to leaks and frequent breaks. In addition, these distribution pipes had issues from tuberculation, but Schuler postulated that the SIPP project has resulted in increased flow for fire protection and other needs.
“
Working with USG was a very good experience. USG was comfortable with the collaborative, hybrid construction approach, being able to use in-kind services from a municipality or utility authority. So it was a very good dynamic in the field. From the office front, the staff we worked with were knowledgeable and professional.
— Eric. G. Schuler, P.E., Director of Engineering, MVWA