Project Summary
San Jose Water Company, CA
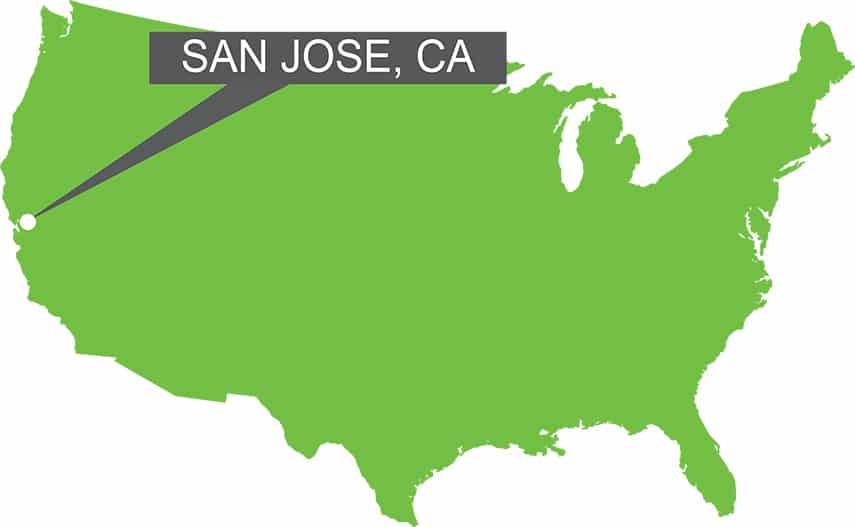
Type of Project
Monoclor® RCS chloramine management system
Results
- Kept stable disinfectant residuals in distribution system in water stressed California
Located on the southern edge of California’s ever-expanding Silicon Valley, the San Jose Water Company treats and distributes water to over 1 million people. Founded in 1866, the investor-owned public utility has built a reputation for being focused on customer service and has been an early adopter of new treatment technologies.
Like many water utilities, San Jose Water has had to adapt to the challenges of using chloramines for secondary disinfection to mitigate potential DBP (disinfection byproduct) formation. Chloramine can be a more stable disinfectant in distribution systems and is formed by reacting aqueous chlorine with ammonia. While the optimal laboratory ratio of chlorine to ammonia is 5:1, “real world” water sources that contain varying levels of ammonia can wreak havoc on residual concentrations.
Getting mix ratios of ammonia and chlorine wrong can not only result in reduced bacterial control in distribution systems, but create nitrification or taste and odor problems as well. Storage tanks pose particular problems to operators as out-of-control chloramine residuals can require a utility to flush or dump an entire tank – an increasingly unacceptable outcome in water stressed California. San Jose Water’s Nitrification Monitoring Program identified the need to boost chloramine residuals in some of its tanks.
“
Getting mix ratios of ammonia and chlorine wrong can result in reduced bacterial control in distribution systems, and can create nitrification and odor problems as well
A chloramine boosting pilot in one of San Jose Water’s 1 million gallon storage tanks was unable to correctly dose the tank with either free chlorine or ammonia to achieve the desired target residuals.
After hearing about the Monoclor® RCS technology for managing chloramine residual, San Jose Water decided to pilot. The Monoclor® RCS chloramine management system tackles the dynamic residual issues by simultaneously controlling three process parameters (1) adding adequate mix energy to the tank volume (2) creating a high energy mix zone for the chlorine and ammonia to fully react and (3) managing the proper mix ratio with a combination of real time sampling and a proprietary dosing algorithm.
A trailer unit was provided for a 3 month trial period. The trailer included a skid-mounted Monoclor® RCS on-site sodium hypochlorite generator that would provide up to 20 pounds per day chlorine (at 0.8% concentration), a liquid ammonium sulfate skid, a chlorine analyzer, and a 15 gallon per minute (GPM) Tank Shark® Eductor Mixer to be placed in the reservoir. By using liquid ammonium sulfate and 0.8% sodium hypochlorite to generate monochloramine, a more stable and safer reactant profile is achieved.
The water booster pump and chemical metering pumps were all located inside the trailer with tubing leading to the reservoir and Tank Shark® Eductor Mixer. With no moving parts or electrical components inside the tank, San Jose Water was able to drop the Tank Shark® Eductor Mixer through the reservoir hatch without confined space entry requirements, divers or taking the tank out of service.
Results were immediate. After reaching and maintaining the desired residual locally for several weeks, San Jose Water increased their target dose and took measures that allowed improved, stable residuals to continue further into the distribution system. The Monoclor® RCS chloramine management system was able to continually maintain the residual through multiple tests for the remainder of the trial.